Analyzing Drill Bit Breakage: Causes, Prevention, and Expert Solutions for Efficient Drilling
- Date:2023-05-28
- Share with:
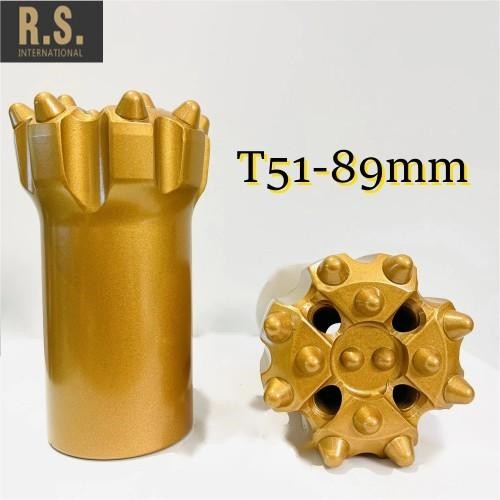
Experiencing frustration due to broken drill bits can hinder progress and increase costs in drilling projects. Therefore, it is crucial to address the underlying causes. Let's explore some common factors:
1.Quality of the Drill Bit:
To avoid drill bit breakage, it is essential to choose a high-quality drill bit that matches the geological formation being drilled. Select a drill bit specifically designed to handle the challenges posed by the specific rock type, hardness, and abrasiveness.
2.Excessive Wear:
Continued use and wear can lead to chipping of drill bits, especially when drilling through softer materials. Regularly inspect the condition of the drill bit and replace it if significant wear is observed. Remember, a worn-out drill bit is more likely to break and compromise drilling performance.
3.Drilling Speed:
Drilling too quickly for the geological conditions can cause shelling of the drill bit, leading to breakage. It is crucial to adjust the drilling speed according to the manufacturer's recommendations and the specific characteristics of the terrain. Adhering to the proper drilling speed ensures better control and minimizes the risk of breakage.
4.Drilling Pressure:
Applying excessive pressure while drilling can cause damage to the drill bit. Achieving the right balance between penetration speed and bit care is essential. Applying the appropriate amount of pressure helps maintain efficiency while preventing unnecessary stress on the bit.
5.Maintenance and Cleaning:
Accumulation of drilling debris on the drill bit can negatively impact its performance and accelerate wear. Regularly clean the drill bit during the drilling process to prevent clogging and optimize its cutting efficiency. Additionally, proper maintenance after each use, such as lubrication and storage in a suitable environment, can extend the life of the drill bit.
In case drill bit breakage persists despite addressing these factors, it is advisable to seek guidance from drilling specialists or consult the manufacturer. They can provide a precise evaluation of the situation and offer tailored solutions based on your specific circumstances.
By understanding the causes and implementing effective prevention techniques, drillers can minimize the risk of drill bit breakage and enhance overall drilling efficiency. I hope the insights shared in this article prove invaluable to all our readers. If you have any further questions or require assistance, please do not hesitate to reach out. As a proud member of RS Rock Drilling, we boast a team of experienced engineers with a wealth of knowledge in drilling operations, committed to providing exceptional service to our valued customers.